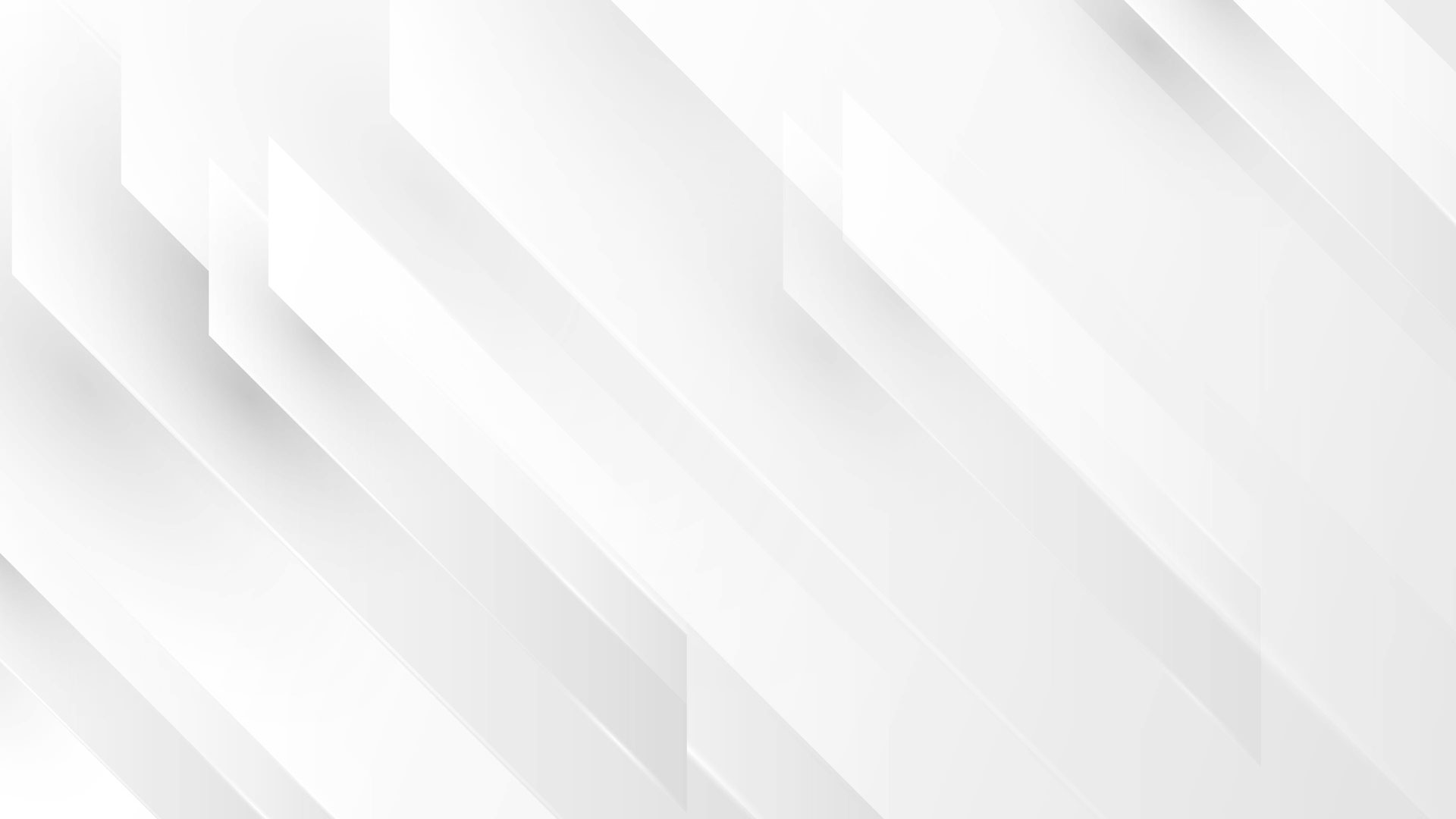
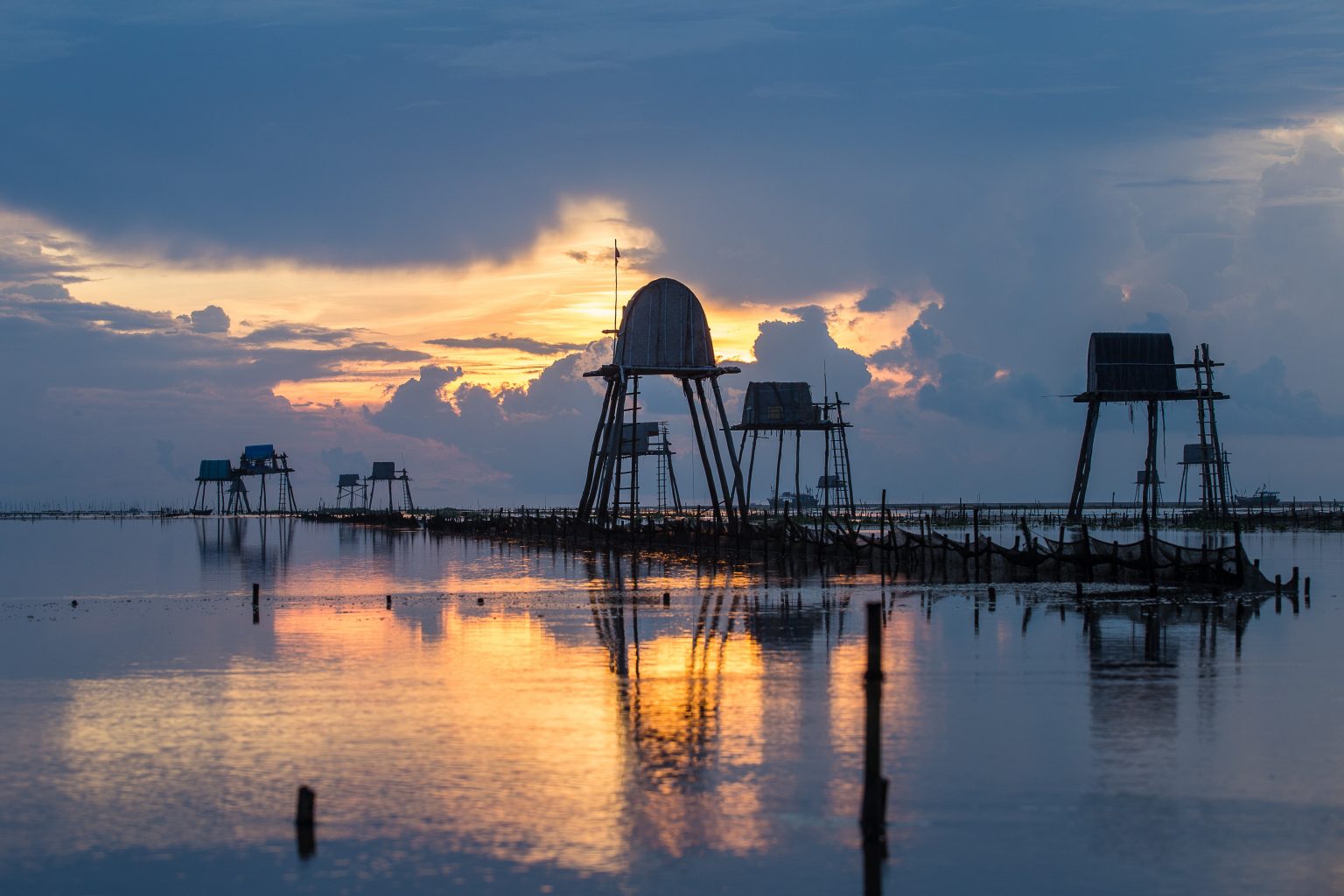
Case Studies
At Amalga Composites, we work with you to build custom solutions. We rely on doctoral-level engineering, a superior manufacturing process, and quality materials to create lightweight, durable, corrosion-resistant composites so you can achieve your goals.
Below are a few examples of how we worked with clients to meet needs, exceed expectations, and deliver incredible results.
May 26, 2022
May 26, 2022
May 26, 2022
May 26, 2022
May 26, 2022
May 26, 2022
May 26, 2022
May 9, 2022